Concrete Lifting 101: A Guide to Restoring Your Concrete
Concrete is everywhere. According to some researchers, it is the second most consumed material in the world. Concrete is used to create driveways, sidewalks, patios, basements, and even entire buildings across the globe.
That is because concrete is incredibly tough and durable.
But even concrete succumbs to the relentless passage of time and the ever-shifting ground beneath it.
Uneven concrete looks terrible, right? It’s also a safety issue, creating tripping hazards and a place for water to pool. Uneven patios or sidewalks may channel water into your basement or foundation, creating even more problems.
Thankfully, there’s a solution! Here at Keystone Gun-Krete, we can lift your concrete back into place without the mess and cost of replacement.
How do we do it, you ask? Great question! Read on to find out how.
What Is Concrete Lifting?
Concrete lifting is just what it sounds like: a process that raises settled concrete slabs back to their original position.
To lift the concrete, our technicians inject a two part polyurethane foam, beneath the slab, filling any voids that have caused it to sink. The material then expands, lifting the slab and stabilizing the surrounding soil.
When Is Concrete Lifting Needed?
Uneven concrete detracts from your property's curb appeal. But that’s not the worst! It also poses safety hazards, especially for anyone with limited mobility.
Several telltale signs indicate that your concrete may need lifting. The most obvious signs are uneven surfaces with dips, slopes, or cracks exceeding half an inch.
Pooling water on your patio or driveway is another sign of a settled slab, which can potentially lead to foundation problems and water damage.
Early intervention is crucial. Like most things, ignoring settled concrete only allows the problem to worsen, increasing the repair cost and risking further damage.
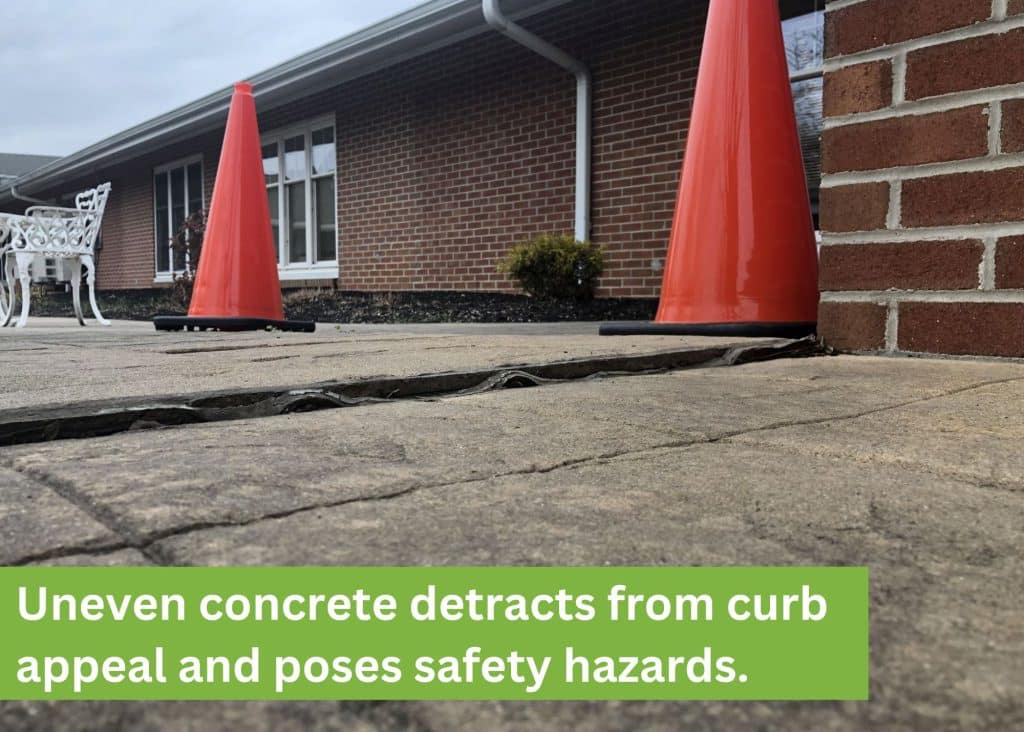
Common areas for concrete to settle include:
- Driveways and sidewalks: These areas present tripping hazards when they sink or become uneven.
- Patios and porches: Settling creates unsightly gaps and uneven surfaces that affect the usability and aesthetics of outdoor living spaces.
- Garage floors: These often experience differential settling, which can affect the structural integrity of the space.
- Industrial and commercial floors: Even minor unevenness in warehouses and other commercial properties can threaten safety and machinery.
NOTE: If your concrete slab is cracked into pieces smaller than a square foot, concrete lifting will likely not be possible. This amount of damage requires complete replacement.
What Causes Concrete to Settle?
Settled concrete is caused by various factors, including:
- Soil Erosion: Over time, water runoff and erosion can wash away the soil beneath the concrete slab, creating voids that cause it to sink.
- Improper Drainage: Poor drainage around the concrete allows water to accumulate and saturate the soil, leading to settlement.
- Tree Root Growth: Tree roots exert tremendous pressure on underground structures, including concrete slabs, causing them to crack and become uneven.
- Construction Faults: Improper compaction of the subgrade during initial construction can lead to uneven settlement over time.
- Freeze-Thaw Cycles: In colder climates, repeated freezing and thawing cycles cause the soil beneath the concrete to expand and contract, eventually leading to settlement.
What does this mean for you?
By identifying the cause of the settled concrete, property owners can take steps to prevent future problems. For instance, addressing drainage issues or removing problematic tree roots can help prevent further settlement after the concrete is lifted.
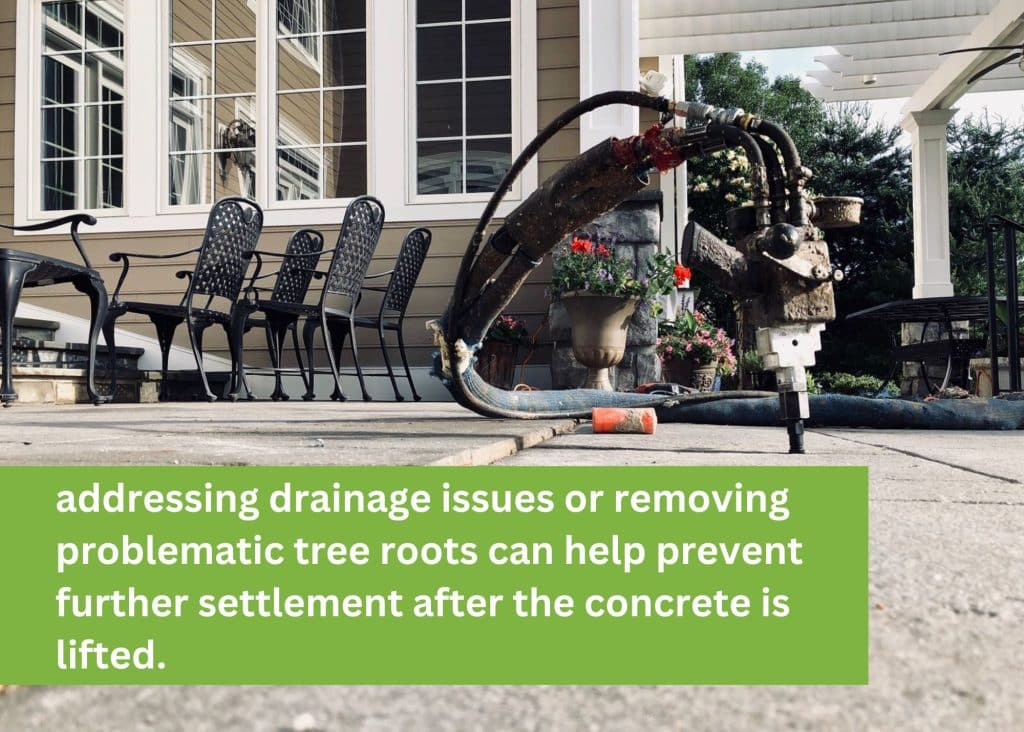
The Process of Concrete Lifting
The concrete lifting process is minimally invasive and can be completed in a single day. Here's a breakdown of the typical steps involved:
- Inspection and Evaluation: A professional concrete lifting contractor assesses the damage. They meticulously examine the unevenness of the concrete, measure the extent of the settlement, and identify the cause (if possible). Based on their evaluation, they recommend the most suitable lifting technique and material for your specific situation.
- Drilling Small Holes: Once a plan is in place, the contractor strategically drills small holes (typically penny-sized) into the concrete slab. The number and placement of these holes depend on the size and severity of the settled area. The contractor carefully spaces these holes to ensure an even lift.
- Material Injection: The contractor injects the two part polyurethane beneath the slab through the drilled holes. The expanding polyurethane foam fills the voids under the concrete, pushing it upward.
- Lifting and Leveling: The contractor monitors and controls the lifting process, carefully regulating the material so the concrete reaches the desired level without over-lifting. Contractors often use leveling equipment for maximum precision.
- Hole Filling and Sealing: Finally, the contractor meticulously fills and seals the injection holes with a material that matches the surrounding concrete. This leaves the surface smooth and virtually invisible, maintaining the aesthetic appeal of your concrete surfaces.
The Benefits of Concrete Lifting
Compared to complete concrete replacement, lifting offers numerous advantages:
- Cost-Effective: Lifting a settled slab is significantly cheaper than removing and replacing the entire concrete surface. It can save you up to 80% on repair costs.
- Faster and Less Disruptive: Concrete lifting is a much quicker process than replacement, typically taking only a day. This minimizes disruption to your daily routine and allows you to use your concrete surfaces sooner.
- Minimal Intrusion: The small injection holes create minimal disruption to your landscaping or surrounding structures.
- Durable Results: When done correctly, concrete lifting provides long-lasting results. Polyurethane foam, for instance, is highly durable and resistant to water and soil erosion.
- Environmentally Friendly: Lifting preserves existing concrete, reducing construction waste and minimizing the environmental impact compared to complete replacement.
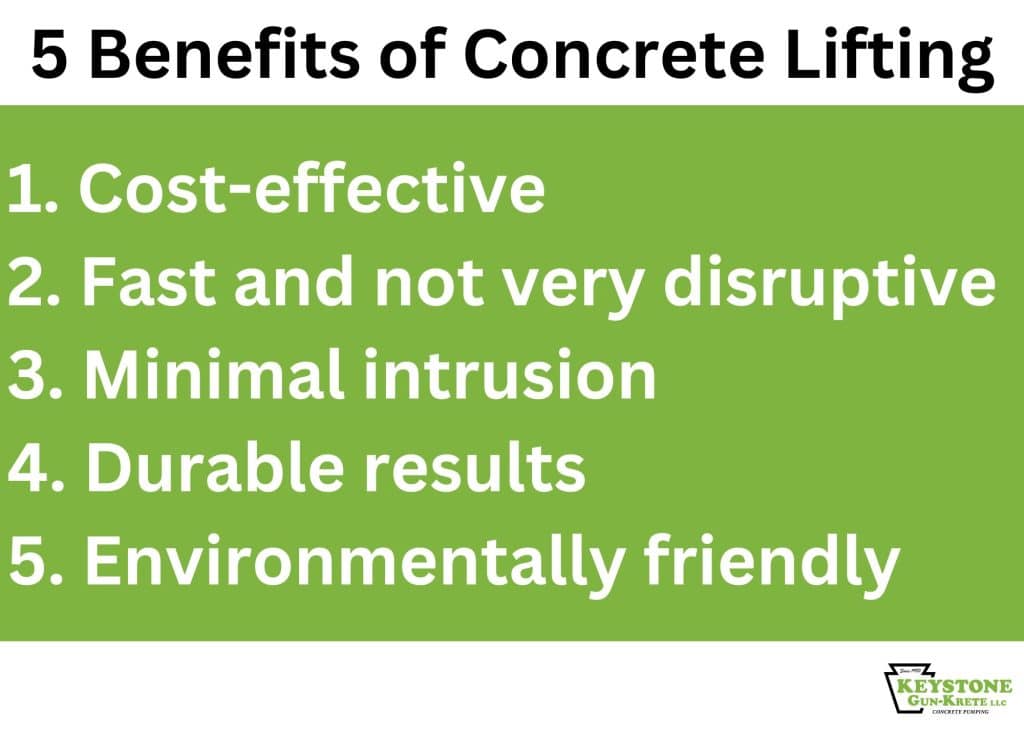
Alternatives (And Why Lifting is Better)
While concrete lifting is the preferred solution for most settled concrete problems, several alternative methods exist: mudjacking, self-leveling compounds, and concrete replacement. Let's explore why lifting remains the champion:
- Mudjacking: This traditional method involves pumping sand, cement, and water beneath the slab. While mudjacking can be cheaper than lifting, it has several drawbacks. The cement mixture is heavy and can cause the slab to sink further over time. Additionally, the large holes required for injection leave unsightly scars, and the process can be messy. Having offered both Mudjacking and Polyurethane lifting over our years of business, the Polyurethane Concrete Lifting has been much more permanent.
- Self-Leveling Compounds: These can be used for minor fixes but are generally unsuitable for addressing more significant issues like severe sinking or large areas. They also add extra weight to the existing slab, which could lead to further accelerated sinking.
- Concrete Replacement: This involves removing the existing slab entirely and pouring new concrete. While effective, replacement is the most expensive and disruptive option. It's a time-consuming process requiring extensive excavation and may necessitate removing landscaping or fixtures.
Conclusion
Simply put, settled concrete detracts from the beauty of your property, poses safety hazards, and leads to further problems.
By partnering with a reputable contractor and implementing preventive measures, you can ensure your concrete surfaces remain strong, stable, and beautiful for years.
Keystone Gun-Krete uses state-of-the-art equipment and materials to ensure a durable and aesthetically pleasing repair. Choosing them guarantees quality workmanship and peace of mind, knowing that the job will be done right the first time.
For a free quote on concrete lifting services in Pennsylvania, Delaware, and Maryland, contact Keystone Gun-Krete, a trusted leader in concrete solutions for over 40 years.
We look forward to working with you!